TPU or Thermoplastic Polyurethane is a commonly used manufacturing material that consists of a mixture of rubber and plastic. Its thermoplastic properties mean it is malleable when heated and solidifies when cooled to room temperature. It’s due to the unique properties and ductility of the material that Studmarc has entire ranges of tactile studs, strips and tactile paving manufactured from TPU.
What is TPU used for?
Thermoplastic polyurethane is used in a wide variety of industries across a vast number of applications owing to its variability and flexibility as a material. The thermoplastic properties of TPU material make it ideal for extrusion and injection moulding. With its thermoplasticity and the material’s composite nature, TPU can possess both hard and soft segments simultaneously. This allows for flexibility and rigidity in the same product which is vital for many of the uses listed below.
Common uses include:
- Instrument Panels (Automotive)
- Power Tools
- Sports Goods
- Shoes
- Mobile Phone Cases
- Inflatable Rafts and Dinghies
- Wire and Cabling
- Jacketing
- Impact Resistant Glass / Glass Lamination
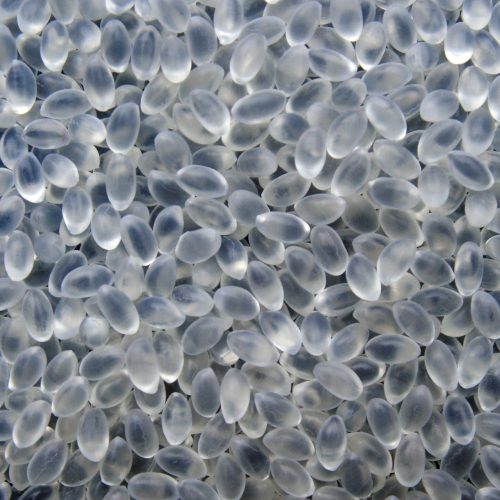
Owing to its flexibility as a thermoplastic, TPU has also proved popular with 3D printer users. It’s often used in powder form that’s heated by the device’s extruder and used as a filament in the printing process.
The characteristics of TPU
There is a wide range of thermoplastic polyurethane compositions and mixtures with different bond structures making it a very versatile material. With the different compositions come different strengths and weaknesses that make them suitable for specific applications.
The characteristics of TPU include:
- High abrasion resistance
- Flexibility at low temperatures
- Chemical resistance
- Malleability when heated to high temperatures
- Microbial resistance
- Oil and grease resistance
- Transparency
- Highly recyclable reducing its environmental impact
- Can be manufactured to be biocompatible, i.e. used in medical applications
- Easy to clean and maintain TPU products
- Mouldable into intricate and delicate patterns or designs
With all of these varying characteristics and the vast compositions of TPU material, it really is a do-it-all material. As thermoplastic polyurethane has become more commonplace there are other materials it’s being substituted in for, such as concrete in the case of tactile paving. Thermoplastic polyurethane also boasts fantastic eco-credentials with its ability to be melted down and recast many times over into different applications.
TPU use in tactile equipment
TPU makes for a fantastic material for studs, strips, and plates due to many of the properties outlined above. Their abrasion resistance ensures longevity and continued tactility underfoot in high-traffic areas, and their oil and grease resistance prevents them from becoming a slip hazard. Thermoplastic polyurethane tactile devices also maintain their colour due to the inherent UV resistance of the material. Maintaining its original colour is vital for a tactile device when used by the blind and visually impaired as they require a contrasting colour to utilise what sight they have available to them.
TPU tactile devices fitting methods vary depending on the product, for tactile studs and strips there is the option of being screwed down with a screw, stuck down with self-adhesive, or fixed in place using epoxy resin. Thermoplastic Polyurethane tactile tiles however can be stuck down with self-adhesive or surface mounted with a specialist adhesive that’s mixed on site and applied.
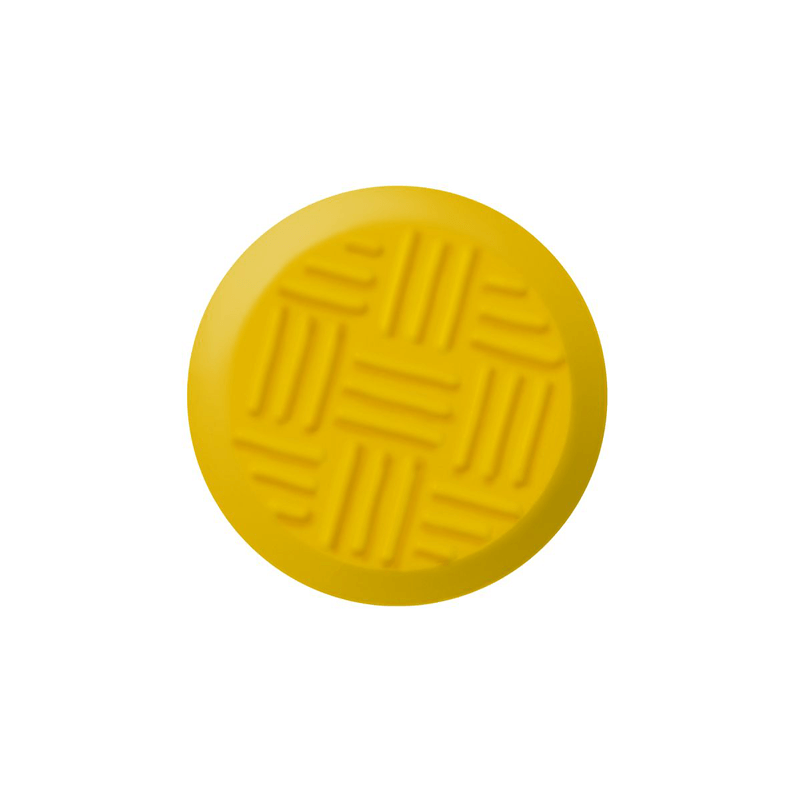
Screw fixing – Ideal for wood or softer surfaces where a screw can get a good purchase. Not suitable in areas where they may be removed due to vandalism or tampering.
Self adhesive – Recommended primarily for indoor installations or areas under cover as the adhesion can be disrupted by rain and other contaminants.
Epoxy resin – The primary method of installation for fixing pin tactile studs and strips. These studs are installed by drilling into the surface to a length just longer than that of the fixing pin and applying an epoxy resin, before inserting that stud or strip. The epoxy resin hardens to a robust level at around 24 hours and can take up to 72 hours to cure completely.
Another way in which TPU is utilised in tactile products is through the use of inserts. Steel studs and strips with textured TPU inserts are great for adding extra grip in variable weather. The added colour customisation of the inserts helps maintain the aesthetic of the surrounding area as well as provides an additional visual cue for those with visual impairments.
Thermoplastic polyurethane tactile equipment has multiple benefits over it’s metal and concrete counterparts:
- Lighter weight
- Less expensive
- TPU tactile paving is more durable when compared to concrete tactile paving
- Easier to replace
- 100% recyclable
- Customisable in a wide range of colours
These advantages make TPU tactile equipment ideal for both permanent and temporary fixtures. The lifespan of TPU tactile indicators will vary depending on the location they’re installed in and the level of foot traffic and contaminants but generally they last for multiple years at a time, seldom needing to be replaced.